What are the Product Standards for Automotive Resistors?
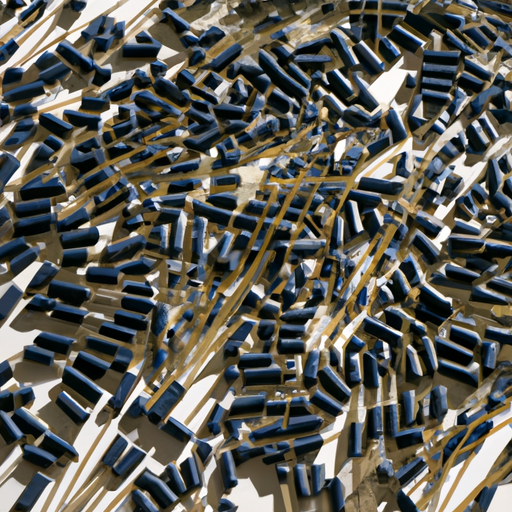
I. Introduction
Automotive resistors are essential components in modern vehicles, playing a critical role in various electronic systems. These components regulate current flow, manage voltage levels, and ensure the proper functioning of sensors and control units. As vehicles become increasingly sophisticated, the importance of reliable and efficient resistors cannot be overstated. To ensure safety, performance, and longevity, automotive resistors must adhere to stringent product standards. This blog post will explore the types of automotive resistors, key standards and regulations, testing and certification processes, performance criteria, challenges in meeting standards, and future trends in automotive resistor standards.
II. Types of Automotive Resistors
Automotive resistors can be categorized into several types, each serving specific functions within a vehicle's electrical system.
A. Fixed Resistors
1. **Carbon Composition Resistors**: These resistors are made from a mixture of carbon and a binding material. They are known for their high energy absorption and are often used in applications where high pulse power is required.
2. **Metal Film Resistors**: These resistors offer better stability and precision compared to carbon composition resistors. They are commonly used in applications requiring high accuracy and low noise.
3. **Wirewound Resistors**: Constructed by winding a metal wire around a ceramic or fiberglass core, wirewound resistors can handle high power levels and are often used in power electronics.
B. Variable Resistors
1. **Potentiometers**: These resistors allow for adjustable resistance and are commonly used in applications such as volume controls and sensor calibration.
2. **Rheostats**: Similar to potentiometers, rheostats are used to control current flow in a circuit. They are typically used in applications requiring high power handling.
C. Specialty Resistors
1. **Power Resistors**: Designed to dissipate significant amounts of power, these resistors are used in applications such as motor control and power supply circuits.
2. **Sensing Resistors**: These resistors are used in current sensing applications, providing feedback to control systems to ensure optimal performance.
III. Key Standards and Regulations
Automotive resistors must comply with various international and national standards to ensure safety and performance.
A. International Standards
1. **ISO (International Organization for Standardization)**: ISO develops and publishes international standards that ensure quality, safety, and efficiency across various industries, including automotive.
2. **IEC (International Electrotechnical Commission)**: IEC standards focus on electrical and electronic technologies, providing guidelines for the design and testing of components like resistors.
B. National Standards
1. **SAE (Society of Automotive Engineers)**: SAE standards are crucial for the automotive industry, providing guidelines for the design, testing, and performance of automotive components, including resistors.
2. **ANSI (American National Standards Institute)**: ANSI oversees the development of voluntary consensus standards for products, services, and systems in the United States, including automotive resistors.
C. Industry-Specific Standards
1. **AEC-Q200 (Automotive Electronics Council)**: This standard outlines the qualification requirements for passive components, including resistors, used in automotive applications, ensuring reliability and performance.
2. **IPC (Institute for Printed Circuits)**: IPC standards focus on the design and manufacturing of printed circuit boards, which often incorporate automotive resistors.
IV. Testing and Certification Processes
To ensure compliance with standards, automotive resistors undergo rigorous testing and certification processes.
A. Overview of Testing Methods
1. **Electrical Testing**: This involves measuring the electrical characteristics of resistors, such as resistance value, tolerance, and power rating, to ensure they meet specified standards.
2. **Environmental Testing**: Resistors are subjected to various environmental conditions, including temperature extremes, humidity, and vibration, to assess their performance and reliability in real-world conditions.
B. Certification Bodies and Their Roles
1. **UL (Underwriters Laboratories)**: UL is a global safety certification organization that tests and certifies products for safety and performance, including automotive resistors.
2. **TUV (Technischer Überwachungsverein)**: TUV provides testing and certification services for a wide range of products, ensuring compliance with international safety and quality standards.
C. Importance of Compliance and Certification
Compliance with established standards and certification by recognized bodies is crucial for manufacturers. It not only ensures product reliability and safety but also enhances consumer confidence and marketability.
V. Performance Criteria for Automotive Resistors
Automotive resistors must meet specific performance criteria to ensure their effectiveness in automotive applications.
A. Electrical Characteristics
1. **Resistance Value Tolerance**: This refers to the allowable deviation from the specified resistance value. High precision is essential in automotive applications to ensure accurate performance.
2. **Temperature Coefficient**: This measures how much the resistance changes with temperature. A low temperature coefficient is desirable to maintain consistent performance across varying temperatures.
3. **Power Rating**: The power rating indicates the maximum power a resistor can dissipate without failure. It is crucial for ensuring that resistors can handle the demands of automotive systems.
B. Environmental Resistance
1. **Temperature Range**: Automotive resistors must operate effectively across a wide temperature range, from extreme cold to high heat, to ensure reliability in diverse conditions.
2. **Humidity and Moisture Resistance**: Resistors must be resistant to moisture and humidity to prevent corrosion and failure, especially in environments prone to water exposure.
3. **Vibration and Shock Resistance**: Given the dynamic nature of automotive environments, resistors must withstand vibrations and shocks without compromising performance.
C. Longevity and Reliability
1. **Aging Effects**: Over time, resistors can experience changes in their electrical characteristics due to aging. Manufacturers must account for these effects in their designs.
2. **Failure Rates and MTBF (Mean Time Between Failures)**: Low failure rates and high MTBF are critical for automotive resistors, as they contribute to the overall reliability of vehicle systems.
VI. Challenges in Meeting Standards
Manufacturers face several challenges in ensuring that automotive resistors meet established standards.
A. Technological Advancements and Their Impact
Rapid advancements in technology can outpace existing standards, necessitating continuous updates and adaptations to ensure compliance.
B. Cost Implications of Compliance
Meeting stringent standards often involves significant investment in testing, materials, and manufacturing processes, which can impact overall production costs.
C. Balancing Performance with Regulatory Requirements
Manufacturers must strike a balance between achieving high performance and adhering to regulatory requirements, which can sometimes conflict.
VII. Future Trends in Automotive Resistor Standards
The automotive industry is evolving, and so are the standards governing automotive resistors.
A. Impact of Electric and Hybrid Vehicles
The rise of electric and hybrid vehicles introduces new challenges and requirements for resistors, necessitating updates to existing standards to accommodate different power management needs.
B. Innovations in Materials and Manufacturing Processes
Advancements in materials science and manufacturing techniques are leading to the development of more efficient and reliable resistors, prompting a reevaluation of current standards.
C. Evolving Regulatory Landscape
As environmental concerns and safety regulations become more stringent, the regulatory landscape for automotive components, including resistors, will continue to evolve.
VIII. Conclusion
In conclusion, automotive resistors are vital components that require adherence to rigorous product standards to ensure safety, performance, and reliability. Manufacturers play a crucial role in ensuring compliance with these standards, which not only enhances product quality but also fosters consumer trust. As the automotive industry continues to evolve, so too will the standards governing automotive resistors, necessitating ongoing innovation and adaptation.
IX. References
1. ISO Standards for Automotive Components
2. IEC Standards for Electrical Components
3. SAE Standards for Automotive Engineering
4. AEC-Q200 Qualification Guidelines
5. IPC Standards for Printed Circuit Boards
This comprehensive overview of automotive resistor standards highlights the importance of these components in modern vehicles and the rigorous processes involved in ensuring their reliability and performance. As technology advances, staying informed about these standards will be crucial for manufacturers and consumers alike.
What are the Product Standards for Automotive Resistors?
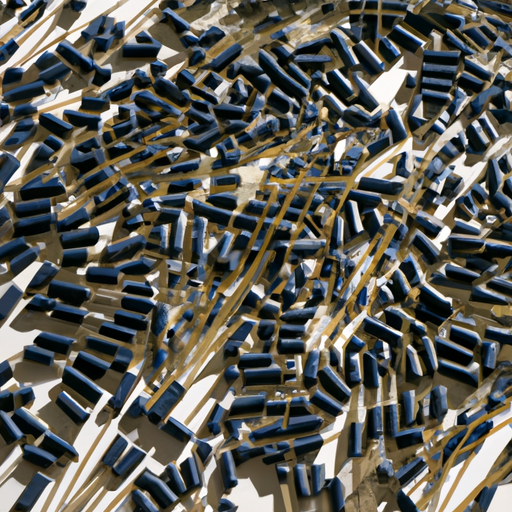
I. Introduction
Automotive resistors are essential components in modern vehicles, playing a critical role in various electronic systems. These components regulate current flow, manage voltage levels, and ensure the proper functioning of sensors and control units. As vehicles become increasingly sophisticated, the importance of reliable and efficient resistors cannot be overstated. To ensure safety, performance, and longevity, automotive resistors must adhere to stringent product standards. This blog post will explore the types of automotive resistors, key standards and regulations, testing and certification processes, performance criteria, challenges in meeting standards, and future trends in automotive resistor standards.
II. Types of Automotive Resistors
Automotive resistors can be categorized into several types, each serving specific functions within a vehicle's electrical system.
A. Fixed Resistors
1. **Carbon Composition Resistors**: These resistors are made from a mixture of carbon and a binding material. They are known for their high energy absorption and are often used in applications where high pulse power is required.
2. **Metal Film Resistors**: These resistors offer better stability and precision compared to carbon composition resistors. They are commonly used in applications requiring high accuracy and low noise.
3. **Wirewound Resistors**: Constructed by winding a metal wire around a ceramic or fiberglass core, wirewound resistors can handle high power levels and are often used in power electronics.
B. Variable Resistors
1. **Potentiometers**: These resistors allow for adjustable resistance and are commonly used in applications such as volume controls and sensor calibration.
2. **Rheostats**: Similar to potentiometers, rheostats are used to control current flow in a circuit. They are typically used in applications requiring high power handling.
C. Specialty Resistors
1. **Power Resistors**: Designed to dissipate significant amounts of power, these resistors are used in applications such as motor control and power supply circuits.
2. **Sensing Resistors**: These resistors are used in current sensing applications, providing feedback to control systems to ensure optimal performance.
III. Key Standards and Regulations
Automotive resistors must comply with various international and national standards to ensure safety and performance.
A. International Standards
1. **ISO (International Organization for Standardization)**: ISO develops and publishes international standards that ensure quality, safety, and efficiency across various industries, including automotive.
2. **IEC (International Electrotechnical Commission)**: IEC standards focus on electrical and electronic technologies, providing guidelines for the design and testing of components like resistors.
B. National Standards
1. **SAE (Society of Automotive Engineers)**: SAE standards are crucial for the automotive industry, providing guidelines for the design, testing, and performance of automotive components, including resistors.
2. **ANSI (American National Standards Institute)**: ANSI oversees the development of voluntary consensus standards for products, services, and systems in the United States, including automotive resistors.
C. Industry-Specific Standards
1. **AEC-Q200 (Automotive Electronics Council)**: This standard outlines the qualification requirements for passive components, including resistors, used in automotive applications, ensuring reliability and performance.
2. **IPC (Institute for Printed Circuits)**: IPC standards focus on the design and manufacturing of printed circuit boards, which often incorporate automotive resistors.
IV. Testing and Certification Processes
To ensure compliance with standards, automotive resistors undergo rigorous testing and certification processes.
A. Overview of Testing Methods
1. **Electrical Testing**: This involves measuring the electrical characteristics of resistors, such as resistance value, tolerance, and power rating, to ensure they meet specified standards.
2. **Environmental Testing**: Resistors are subjected to various environmental conditions, including temperature extremes, humidity, and vibration, to assess their performance and reliability in real-world conditions.
B. Certification Bodies and Their Roles
1. **UL (Underwriters Laboratories)**: UL is a global safety certification organization that tests and certifies products for safety and performance, including automotive resistors.
2. **TUV (Technischer Überwachungsverein)**: TUV provides testing and certification services for a wide range of products, ensuring compliance with international safety and quality standards.
C. Importance of Compliance and Certification
Compliance with established standards and certification by recognized bodies is crucial for manufacturers. It not only ensures product reliability and safety but also enhances consumer confidence and marketability.
V. Performance Criteria for Automotive Resistors
Automotive resistors must meet specific performance criteria to ensure their effectiveness in automotive applications.
A. Electrical Characteristics
1. **Resistance Value Tolerance**: This refers to the allowable deviation from the specified resistance value. High precision is essential in automotive applications to ensure accurate performance.
2. **Temperature Coefficient**: This measures how much the resistance changes with temperature. A low temperature coefficient is desirable to maintain consistent performance across varying temperatures.
3. **Power Rating**: The power rating indicates the maximum power a resistor can dissipate without failure. It is crucial for ensuring that resistors can handle the demands of automotive systems.
B. Environmental Resistance
1. **Temperature Range**: Automotive resistors must operate effectively across a wide temperature range, from extreme cold to high heat, to ensure reliability in diverse conditions.
2. **Humidity and Moisture Resistance**: Resistors must be resistant to moisture and humidity to prevent corrosion and failure, especially in environments prone to water exposure.
3. **Vibration and Shock Resistance**: Given the dynamic nature of automotive environments, resistors must withstand vibrations and shocks without compromising performance.
C. Longevity and Reliability
1. **Aging Effects**: Over time, resistors can experience changes in their electrical characteristics due to aging. Manufacturers must account for these effects in their designs.
2. **Failure Rates and MTBF (Mean Time Between Failures)**: Low failure rates and high MTBF are critical for automotive resistors, as they contribute to the overall reliability of vehicle systems.
VI. Challenges in Meeting Standards
Manufacturers face several challenges in ensuring that automotive resistors meet established standards.
A. Technological Advancements and Their Impact
Rapid advancements in technology can outpace existing standards, necessitating continuous updates and adaptations to ensure compliance.
B. Cost Implications of Compliance
Meeting stringent standards often involves significant investment in testing, materials, and manufacturing processes, which can impact overall production costs.
C. Balancing Performance with Regulatory Requirements
Manufacturers must strike a balance between achieving high performance and adhering to regulatory requirements, which can sometimes conflict.
VII. Future Trends in Automotive Resistor Standards
The automotive industry is evolving, and so are the standards governing automotive resistors.
A. Impact of Electric and Hybrid Vehicles
The rise of electric and hybrid vehicles introduces new challenges and requirements for resistors, necessitating updates to existing standards to accommodate different power management needs.
B. Innovations in Materials and Manufacturing Processes
Advancements in materials science and manufacturing techniques are leading to the development of more efficient and reliable resistors, prompting a reevaluation of current standards.
C. Evolving Regulatory Landscape
As environmental concerns and safety regulations become more stringent, the regulatory landscape for automotive components, including resistors, will continue to evolve.
VIII. Conclusion
In conclusion, automotive resistors are vital components that require adherence to rigorous product standards to ensure safety, performance, and reliability. Manufacturers play a crucial role in ensuring compliance with these standards, which not only enhances product quality but also fosters consumer trust. As the automotive industry continues to evolve, so too will the standards governing automotive resistors, necessitating ongoing innovation and adaptation.
IX. References
1. ISO Standards for Automotive Components
2. IEC Standards for Electrical Components
3. SAE Standards for Automotive Engineering
4. AEC-Q200 Qualification Guidelines
5. IPC Standards for Printed Circuit Boards
This comprehensive overview of automotive resistor standards highlights the importance of these components in modern vehicles and the rigorous processes involved in ensuring their reliability and performance. As technology advances, staying informed about these standards will be crucial for manufacturers and consumers alike.