The Production Process of Mainstream Fuse Resistors
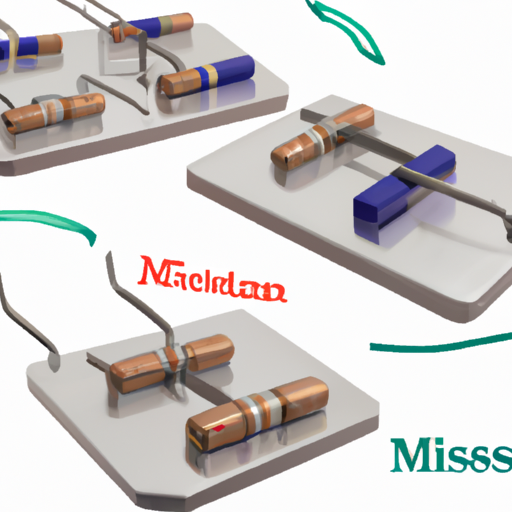
I. Introduction
In the realm of electrical engineering, fuse resistors play a pivotal role in ensuring the safety and reliability of electrical circuits. These components not only provide resistance but also serve as protective devices that prevent overcurrent situations, which can lead to circuit damage or failure. This blog post will delve into the production process of mainstream fuse resistors, exploring their functionality, the materials used, and the intricate steps involved in their manufacturing.
II. Understanding Fuse Resistors
A. Functionality and Applications
Fuse resistors are designed to protect electrical circuits from excessive current. When the current exceeds a predetermined level, the fuse resistor will "blow," effectively interrupting the circuit and preventing further damage. This functionality is crucial in various applications, including automotive systems, consumer electronics, and telecommunications equipment. By integrating fuse resistors into these systems, manufacturers can enhance safety and reliability.
B. Types of Fuse Resistors
There are several types of fuse resistors, each with unique characteristics suited for different applications:
1. **Wirewound Fuse Resistors**: These resistors are made by winding a resistive wire around a ceramic or insulating core. They are known for their high power ratings and stability under varying temperatures.
2. **Thick Film Fuse Resistors**: These resistors are created by applying a thick film of resistive material onto a substrate. They are often used in surface-mount technology (SMT) applications due to their compact size.
3. **Thin Film Fuse Resistors**: Similar to thick film resistors, thin film resistors utilize a much thinner layer of resistive material. They offer high precision and stability, making them ideal for high-frequency applications.
III. Raw Materials Used in Fuse Resistor Production
The production of fuse resistors requires a variety of raw materials, each contributing to the overall performance and reliability of the final product.
A. Conductive Materials
1. **Metal Alloys**: Commonly used metal alloys include nickel-chromium and copper. These materials provide the necessary conductivity and thermal stability required for effective resistance.
2. **Carbon-based Materials**: Carbon is often used in the production of thick film resistors due to its excellent conductive properties and cost-effectiveness.
B. Insulating Materials
1. **Ceramics**: Ceramic materials are widely used for their excellent insulating properties and ability to withstand high temperatures.
2. **Epoxy Resins**: These resins are used for encapsulating components, providing additional insulation and protection against environmental factors.
C. Additional Components
1. **Protective Coatings**: These coatings are applied to enhance durability and protect against moisture, dust, and other contaminants.
2. **Terminals and Connectors**: Essential for integrating the fuse resistor into electrical circuits, these components ensure reliable connections.
IV. The Production Process
The production of fuse resistors involves several key steps, each critical to ensuring the quality and performance of the final product.
A. Design and Prototyping
The first step in the production process is the design and prototyping phase. Engineers define the electrical specifications, such as resistance values and voltage ratings, and consider mechanical design aspects to ensure the resistor can withstand operational stresses.
B. Material Preparation
Once the design is finalized, the next step is material preparation. This involves sourcing high-quality raw materials and conducting quality control checks to ensure they meet industry standards. Pre-processing of materials, such as cutting and shaping, is also performed to prepare them for manufacturing.
C. Manufacturing Steps
1. **Forming the Resistor Element**:
- **Wirewound Techniques**: In this method, a resistive wire is wound around a core, which is then secured and insulated.
- **Thick and Thin Film Techniques**: For thick film resistors, a paste of resistive material is screen-printed onto a substrate. In contrast, thin film resistors involve depositing a very thin layer of resistive material using vacuum deposition techniques.
2. **Assembly of Components**:
- **Mounting the Resistor Element**: The formed resistor element is mounted onto a base or substrate.
- **Adding Insulation and Protective Coatings**: Insulating materials are applied to protect the resistor from environmental factors, followed by the application of protective coatings.
3. **Integration of Terminals and Connectors**: Finally, terminals and connectors are integrated into the assembly, ensuring that the fuse resistor can be easily connected to electrical circuits.
D. Testing and Quality Assurance
Quality assurance is a critical step in the production process. Various tests are conducted to ensure the fuse resistors meet the required specifications:
1. **Electrical Testing**: This includes measuring resistance values and verifying voltage ratings to ensure the component functions correctly under operational conditions.
2. **Mechanical Testing**: Durability and thermal stability tests are performed to assess the resistor's ability to withstand physical stresses and temperature variations.
3. **Compliance with Industry Standards**: Manufacturers must ensure that their products comply with relevant industry standards, such as those set by the International Electrotechnical Commission (IEC) and Underwriters Laboratories (UL).
V. Post-Production Processes
After the manufacturing and testing phases, several post-production processes are undertaken to prepare the fuse resistors for market distribution.
A. Packaging and Labeling
Proper packaging is essential to protect the resistors during transportation and storage. Each package is labeled with important information, including specifications, safety warnings, and compliance certifications.
B. Inventory Management
Efficient inventory management ensures that products are readily available for distribution while minimizing excess stock. This involves tracking production batches and managing stock levels.
C. Distribution Channels
Fuse resistors are distributed through various channels, including direct sales to manufacturers, electronic component distributors, and online marketplaces. Establishing strong relationships with distributors is crucial for reaching a broader customer base.
VI. Challenges in Fuse Resistor Production
The production of fuse resistors is not without its challenges. Manufacturers face several hurdles that can impact production efficiency and product quality.
A. Material Sourcing and Cost Fluctuations
The availability and cost of raw materials can fluctuate due to market conditions, affecting production costs and timelines. Manufacturers must develop strategies to mitigate these risks, such as establishing long-term supplier relationships.
B. Technological Advancements and Adaptation
As technology evolves, manufacturers must adapt to new production techniques and materials. Staying ahead of industry trends is essential for maintaining competitiveness.
C. Environmental Considerations and Sustainability
With increasing awareness of environmental issues, manufacturers are under pressure to adopt sustainable practices. This includes reducing waste, recycling materials, and minimizing the environmental impact of production processes.
VII. Future Trends in Fuse Resistor Production
The future of fuse resistor production is likely to be shaped by several key trends:
A. Innovations in Materials and Manufacturing Techniques
Advancements in materials science may lead to the development of new conductive and insulating materials that enhance performance and reduce costs. Additionally, innovative manufacturing techniques, such as additive manufacturing, could revolutionize the production process.
B. The Role of Automation and Industry 4.0
The integration of automation and smart manufacturing technologies will streamline production processes, improve efficiency, and reduce human error. Industry 4.0 principles, such as data analytics and IoT, will enable manufacturers to optimize operations and enhance product quality.
C. Increasing Demand for Miniaturization and Efficiency
As electronic devices continue to shrink in size, the demand for compact and efficient fuse resistors will grow. Manufacturers will need to focus on developing smaller, high-performance components that meet the needs of modern applications.
VIII. Conclusion
In conclusion, fuse resistors are essential components in electrical circuits, providing critical overcurrent protection across various industries. The production process of these devices is complex, involving careful design, material selection, and rigorous testing to ensure quality and reliability. As the industry evolves, manufacturers must navigate challenges while embracing innovations that will shape the future of fuse resistor production. By understanding the intricacies of this process, we can appreciate the vital role that fuse resistors play in safeguarding our electrical systems.
The Production Process of Mainstream Fuse Resistors
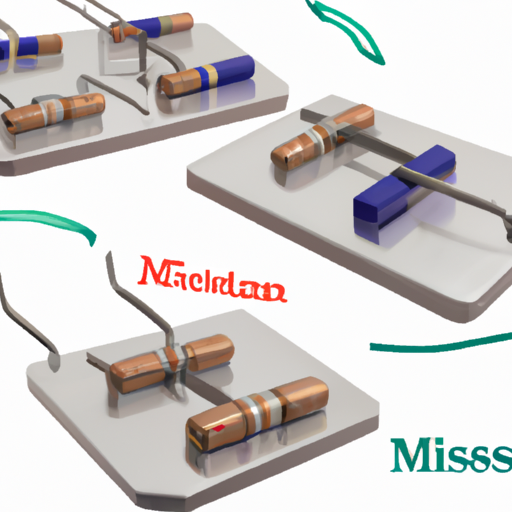
I. Introduction
In the realm of electrical engineering, fuse resistors play a pivotal role in ensuring the safety and reliability of electrical circuits. These components not only provide resistance but also serve as protective devices that prevent overcurrent situations, which can lead to circuit damage or failure. This blog post will delve into the production process of mainstream fuse resistors, exploring their functionality, the materials used, and the intricate steps involved in their manufacturing.
II. Understanding Fuse Resistors
A. Functionality and Applications
Fuse resistors are designed to protect electrical circuits from excessive current. When the current exceeds a predetermined level, the fuse resistor will "blow," effectively interrupting the circuit and preventing further damage. This functionality is crucial in various applications, including automotive systems, consumer electronics, and telecommunications equipment. By integrating fuse resistors into these systems, manufacturers can enhance safety and reliability.
B. Types of Fuse Resistors
There are several types of fuse resistors, each with unique characteristics suited for different applications:
1. **Wirewound Fuse Resistors**: These resistors are made by winding a resistive wire around a ceramic or insulating core. They are known for their high power ratings and stability under varying temperatures.
2. **Thick Film Fuse Resistors**: These resistors are created by applying a thick film of resistive material onto a substrate. They are often used in surface-mount technology (SMT) applications due to their compact size.
3. **Thin Film Fuse Resistors**: Similar to thick film resistors, thin film resistors utilize a much thinner layer of resistive material. They offer high precision and stability, making them ideal for high-frequency applications.
III. Raw Materials Used in Fuse Resistor Production
The production of fuse resistors requires a variety of raw materials, each contributing to the overall performance and reliability of the final product.
A. Conductive Materials
1. **Metal Alloys**: Commonly used metal alloys include nickel-chromium and copper. These materials provide the necessary conductivity and thermal stability required for effective resistance.
2. **Carbon-based Materials**: Carbon is often used in the production of thick film resistors due to its excellent conductive properties and cost-effectiveness.
B. Insulating Materials
1. **Ceramics**: Ceramic materials are widely used for their excellent insulating properties and ability to withstand high temperatures.
2. **Epoxy Resins**: These resins are used for encapsulating components, providing additional insulation and protection against environmental factors.
C. Additional Components
1. **Protective Coatings**: These coatings are applied to enhance durability and protect against moisture, dust, and other contaminants.
2. **Terminals and Connectors**: Essential for integrating the fuse resistor into electrical circuits, these components ensure reliable connections.
IV. The Production Process
The production of fuse resistors involves several key steps, each critical to ensuring the quality and performance of the final product.
A. Design and Prototyping
The first step in the production process is the design and prototyping phase. Engineers define the electrical specifications, such as resistance values and voltage ratings, and consider mechanical design aspects to ensure the resistor can withstand operational stresses.
B. Material Preparation
Once the design is finalized, the next step is material preparation. This involves sourcing high-quality raw materials and conducting quality control checks to ensure they meet industry standards. Pre-processing of materials, such as cutting and shaping, is also performed to prepare them for manufacturing.
C. Manufacturing Steps
1. **Forming the Resistor Element**:
- **Wirewound Techniques**: In this method, a resistive wire is wound around a core, which is then secured and insulated.
- **Thick and Thin Film Techniques**: For thick film resistors, a paste of resistive material is screen-printed onto a substrate. In contrast, thin film resistors involve depositing a very thin layer of resistive material using vacuum deposition techniques.
2. **Assembly of Components**:
- **Mounting the Resistor Element**: The formed resistor element is mounted onto a base or substrate.
- **Adding Insulation and Protective Coatings**: Insulating materials are applied to protect the resistor from environmental factors, followed by the application of protective coatings.
3. **Integration of Terminals and Connectors**: Finally, terminals and connectors are integrated into the assembly, ensuring that the fuse resistor can be easily connected to electrical circuits.
D. Testing and Quality Assurance
Quality assurance is a critical step in the production process. Various tests are conducted to ensure the fuse resistors meet the required specifications:
1. **Electrical Testing**: This includes measuring resistance values and verifying voltage ratings to ensure the component functions correctly under operational conditions.
2. **Mechanical Testing**: Durability and thermal stability tests are performed to assess the resistor's ability to withstand physical stresses and temperature variations.
3. **Compliance with Industry Standards**: Manufacturers must ensure that their products comply with relevant industry standards, such as those set by the International Electrotechnical Commission (IEC) and Underwriters Laboratories (UL).
V. Post-Production Processes
After the manufacturing and testing phases, several post-production processes are undertaken to prepare the fuse resistors for market distribution.
A. Packaging and Labeling
Proper packaging is essential to protect the resistors during transportation and storage. Each package is labeled with important information, including specifications, safety warnings, and compliance certifications.
B. Inventory Management
Efficient inventory management ensures that products are readily available for distribution while minimizing excess stock. This involves tracking production batches and managing stock levels.
C. Distribution Channels
Fuse resistors are distributed through various channels, including direct sales to manufacturers, electronic component distributors, and online marketplaces. Establishing strong relationships with distributors is crucial for reaching a broader customer base.
VI. Challenges in Fuse Resistor Production
The production of fuse resistors is not without its challenges. Manufacturers face several hurdles that can impact production efficiency and product quality.
A. Material Sourcing and Cost Fluctuations
The availability and cost of raw materials can fluctuate due to market conditions, affecting production costs and timelines. Manufacturers must develop strategies to mitigate these risks, such as establishing long-term supplier relationships.
B. Technological Advancements and Adaptation
As technology evolves, manufacturers must adapt to new production techniques and materials. Staying ahead of industry trends is essential for maintaining competitiveness.
C. Environmental Considerations and Sustainability
With increasing awareness of environmental issues, manufacturers are under pressure to adopt sustainable practices. This includes reducing waste, recycling materials, and minimizing the environmental impact of production processes.
VII. Future Trends in Fuse Resistor Production
The future of fuse resistor production is likely to be shaped by several key trends:
A. Innovations in Materials and Manufacturing Techniques
Advancements in materials science may lead to the development of new conductive and insulating materials that enhance performance and reduce costs. Additionally, innovative manufacturing techniques, such as additive manufacturing, could revolutionize the production process.
B. The Role of Automation and Industry 4.0
The integration of automation and smart manufacturing technologies will streamline production processes, improve efficiency, and reduce human error. Industry 4.0 principles, such as data analytics and IoT, will enable manufacturers to optimize operations and enhance product quality.
C. Increasing Demand for Miniaturization and Efficiency
As electronic devices continue to shrink in size, the demand for compact and efficient fuse resistors will grow. Manufacturers will need to focus on developing smaller, high-performance components that meet the needs of modern applications.
VIII. Conclusion
In conclusion, fuse resistors are essential components in electrical circuits, providing critical overcurrent protection across various industries. The production process of these devices is complex, involving careful design, material selection, and rigorous testing to ensure quality and reliability. As the industry evolves, manufacturers must navigate challenges while embracing innovations that will shape the future of fuse resistor production. By understanding the intricacies of this process, we can appreciate the vital role that fuse resistors play in safeguarding our electrical systems.